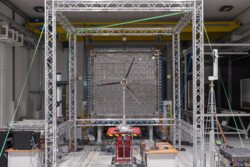
Scientists at Jade University and the University of Oldenburg are investigating the behavior of wind turbines in turbulent wind flows. In order to investigate the deformations of rotating rotor blades, various measurement techniques have now been successfully combined. The TurbuMetric project is funded by the European Regional Development Fund (ERDF).
Due to turbulent wind flows, a wide variety of forces are permanently acting on wind turbines. These lead to frequent load changes and thus to unintentional material fatigue and damage, which in turn leads to a reduction in operating time or unplanned maintenance work. In order to gain a better understanding of the interaction of blade deformations and wind flows during operation, combined experiments have now been conducted in the turbulence wind tunnel for the first time. "In this interdisciplinary research work in the turbulence wind tunnel, flow measurement techniques and optical deformation measurement techniques are merged, resulting in comprehensive information about the couplings", explains Prof. Dr. Thomas Luhmann.
The experiments took place in the turbulence wind tunnel of the University of Oldenburg, which allows the controlled generation of different turbulent wind situations. A three-bladed model turbine with a blade length of 90 cm is used as a wind turbine model. To ensure that the aerodynamic properties correspond to those of real turbines, the turbine rotates at up to 480 revolutions per minute. Therefore, only highly dynamic measuring systems can be used for the observation, explains Dr. Gerd Gülker from ForWind at the Institute of Physics, who heads the subproject on the university side. Furthermore, neither the wind flow nor the blade geometry may be changed by tactile measuring systems during the experiments, as this would falsify the results, Gülker adds.
The scientists are therefore using a high-speed stereo PIV (Particle Imaging Velocimetry) system for the non-contact measurement of the wind flow around the blade. By comparing this data with the inflow, which was obtained using Laser Doppler Anemometry (LDA), the effects of the turbulent wind flow on the plant can be determined. This information is combined with the data of a high-speed photogrammetry system, which determines planar information about the deformations that occur. For this purpose, a measurement concept was developed which reconstructs the surface with high accuracy and a three-dimensional object resolution of up to 0.5 mm.
By combining the individual results in space and time, the researchers can gain new insights into the complex interaction of wind and rotor blade and thus propose new strategies for minimizing loads in turbulent wind flows. Further information can be found at www.turbumetric.de.
Picture: Lars Kröger, ForWind, University of Oldenburg; text: Jade University of Applied Sciences Wilhelmshaven/Oldenburg/Elsfleth
Translated with www.DeepL.com/Translator (free version)